Automating safety and efficiency in Eaton's paint line operations
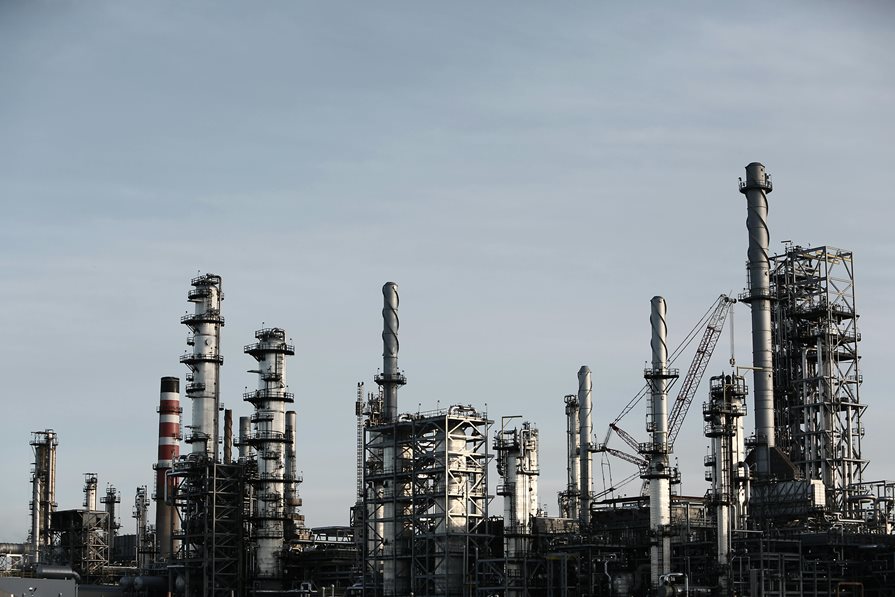
Colleen McCann, Smart Centre, Cris Pop, School of Engineering & Technology
Eaton’s Milton facility faced a critical challenge in managing the manual loading and unloading of its paint line, especially with larger, heavier parts that presented safety risks for operators. Given the varying dimensions and weights of parts in their product line, a fully automated solution was impractical for the wide range of components they produce. Operators struggled with parts weighing up to 150 pounds and measuring up to 98 inches, increasing the risk of ergonomic injuries. This project set out to find a safe and efficient approach to streamline the paint line process and reduce physical strain for operators.
To address this, the project focused on implementing a partial automation solution targeting the most hazardous parts. By integrating robotic and vision systems to manage the heavier and more complex components, operators could focus on handling smaller parts. This approach not only significantly reduced the need for physical handling of larger items but also kept costs lower than a fully automated solution. Additionally, the project will provide Eaton with budgetary recommendations, enabling them to plan for future capital investments as they scale their automation initiatives.
We acknowledge the support of the Natural Sciences and Engineering Research Council of Canada (NSERC).